
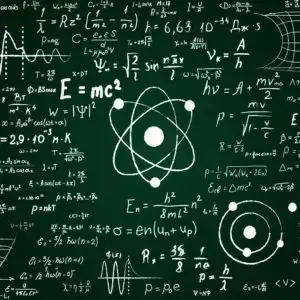
The typical cause of this is a biomarker sticks to one side of an embryo, marking it as left (or right, I don’t remember), but a twin embryo that is too close will see that marker on the other side and develop mirror imaged to the first embryo, right?
The business strategy decisions behind CPU fab is really interesting over the past 15 years.
AMD made a budget clone of Intel two decades ago. Then Intel made a misstep and released Northwood Pentium 4. AMD used less power and was faster. And AMD decided to go with DDR memory, while Intel went RDRAM. Then AMD was king when they went AMDx86-64 for 64 bit and Intel went Itanium.
Then AMD made a huge miscalculation on the future of multicore computing and designed Bulldozer, while Intel got their shit together and went down the hyperthreading route and released CORE/Core2/Core2Duo chips. And Intel was king for a decade.
I don’t know the exact timing, but AMD needed cash and sold their fabs to raise money, which became
TSMCGlobalFoundries, sorry. GF learned how to make stuff small since smartphones became a huge market. Then AMD let an engineer run the company and she invested in the Zen architecture, which could be made by GF with their lessons from the mobile world.This is my take. By AMD turning GF loose, GF could
date other peoplework on mobile projects, which helped them learn.It’s a side note now, but Intel hung on to their fabs and lagged behind GF. AMD let their fab go and benefitted from it. EDIT: I had some facts wrong. It’s possible Intel fabs are ahead of GF.
As a side note, Intel did try fairly hard to get into mobile like GF. They had the Atom chips and went for tablet, Ultrabook, netbook, and mobile. I had an ASUS Android phone with an Intel SOC. So it’s not like they ignored mobile, but it didn’t benefit them as much as TSMC.